Plate heat exchangers were firstly available to the general public in 1920. Their use ever since has grown exponentially across multiple industries and applications. But what is an industrial plate heat exchanger? A plate exchanger is made out of multiple parallel placed plates, one on top of another, to allow fluids to freely flow between them. The space between every two plates is the space where the fluid flows. On each corner of each plate, there are holes (4 in total on each plate).
These holes allow hot and cold fluid to move through alternating channels inside the exchanger. This way, a plate is always in contact with one side being hot and the other being cold. The fluid is mixed, making contact with both hot and cold plates.
Each plate of an industrial heat exchanger can vary in size. It can be anything from as little as 100 mm x 300 mm to up to 3 square meters. The latter is the size of most industrial heat exchangers. Most industrial exchangers have up to 100 and more plates, and as little as 10. Sometimes, these exchangers can cover areas up to thousands of square meters.
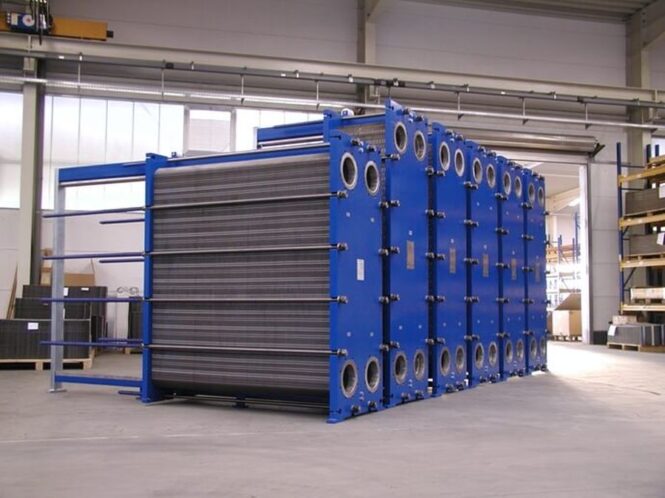
The plates on the exchanger are corrugated to increase the thermal exchange surface, provide mechanical rigidity to the exchanger, and increase the turbulence of the exchanger. In most cases, these plates can be made out of stainless steel, titanium, and aluminum.
The corrugation of the plates forces the fluids inside to move on a tortuous path and setting up to 5 millimeters of space between each plate.
The fluids can cross by eighter in series, or by making counter-current or current configurations.
Main Characteristics of Plate Heat Exchangers
Usually, the maximum temperature needed for sealing heat exchangers is between 80-degrees Celsius and 200-degrees Celsius. The pressure inside of most plate heat exchangers can reach up to 25 bars, according to exodraft-heatrecovery.com.
Some of the main characteristics of industrial plate heat exchangers are:
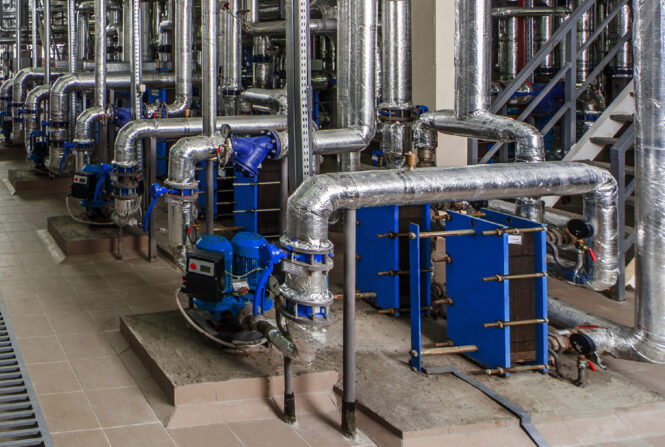
- The plates and parts of the exchanger are very easy to install, uninstall, clean, and control.
- The thermal flow of operations can be easily increased or decreased by adding or removing the plates.
- Fluid leaks are not something uncommon with industrial plate heat exchangers. They mostly appear due to the non-perfect sealing of the gaskets. If a leak occurs, then that plate is contaminated, but contamination of the other fluids is not possible since other fluids are directed away in the case of a leak.
- Often times, materials that are poorly adapted to soldering, such as titanium, can be used in plate heat exchangers.
- Each gasket of the plate heat exchanger limits the maximum pressure and temperature value of the plates.
- The production process of these exchangers is quite difficult and complex. This is why most industrial plate heat exchangers are quite costly. The most expensive part of the entire exchanger is not the plate, but the gaskets.
- The gaskets are what seal the frames which are created by the continued pressing of the plates.