Bead mills, an integral part of many industrial processes, play a crucial role in grinding and dispersion applications across various sectors such as paint, pharmaceuticals, agrochemicals, and cosmetics. By understanding what is a bead mill and the workings of both horizontal and vertical constructions, you can maximize efficiency and achieve superior results.
Bead Mill Working Principle
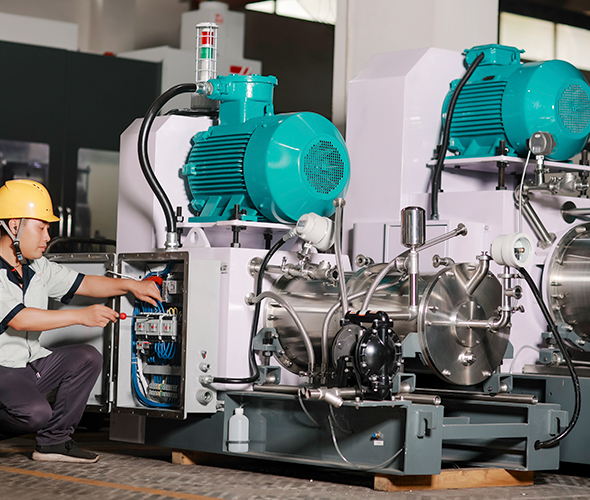
A bead mill method of processing functions by administering an agitation or stirring effect on grinding media (beads) within a cylindrical container to pulverize or spread particles. This rotor-induced movement results in a strong shear force and collision effect on the particles. This equipment is ideally suited to process bigger particles through grinding and facilitates the dispersion of nanoparticles. By carefully calibrating media size, rotor speed, and the type of rotor, the degree of energy and impact force can be tailored to establish the most suitable conditions for every unique material.
Media size and material have a significant effect on how a bead mill work. Large ones (greater than 0.5 mm) are excellent for grinding micron-size particles into submicron-size ones. Small ones (0.3 mm or smaller) are better suited for grinding or dispersing submicron- or nanometer-size particles.
Horizontal Bead Mills Working Principle
Horizontal machines feature a horizontal tubular grinding chamber with an agitator shaft and disks. Energy is transferred from the disk to the fluid in the mill, and the product is sheared by the media’s surface rather than by the disks. This design allows for the efficient use of small amounts of media, its size flexibility, a significant reduction in product loss, maximum color strength, gloss durability, yield, and consistent performance.
The efficiency of such machines is influenced by factors such as the rotor speed, bead size and type used, and the hardness of the particles. Despite this, the horizontal type of mills is extensively employed in such industries as paint and ink, pharmaceuticals, cosmetics, and food processing.
Vertical Bead Mill Working Principle
Vertical machines consist of a large vertical grinding chamber with a centrally located agitator and several grinding disks. The premix material enters from the bottom, is sheared by the rotating disks, and exits through a separation device at the top.
Despite being capable of precision tasks like drilling, fly cutting, boring, and milling, the vertical machines can be constrained by media volume charge and fluidizing issues related to the use of finer grinding media. Furthermore, the finished particle size is often limited to approximately 5 microns.
Industries such as ceramic inks, digital inks, pigment processing, and more commonly use vertical bead mills.
Comparison between Horizontal and Vertical Bead Mills
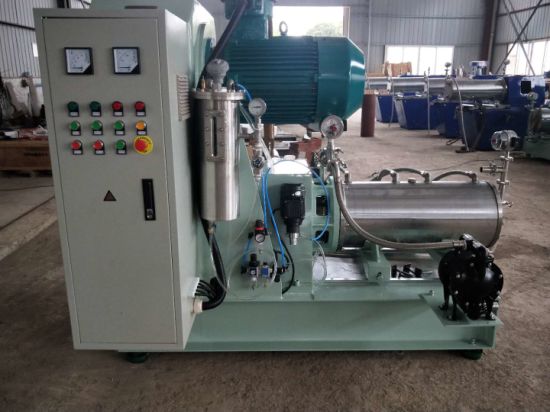
When considering milling equipment for a particular application, a fundamental decision is the orientation of the construction – whether vertical or horizontal. Each type presents unique attributes and benefits depending on the specific use case.
Vertical
Vertical mills comprise a centrally located agitator with several grinding disks on a vertical axis. The grinding chamber houses the agitator and a balance pulley at the base, which guides the product flow. This configuration allows precise tasks like drilling, boring, milling, and fly cutting. The material enters at the bottom, undergoes shearing by the rotating disks, and exits through a separation device at the top.
However, vertical machines also have limitations. Their design makes them less suitable for loading with high media volume, primarily due to gravity-induced media flotation and abrasion. Additionally, obtaining ultra-fine particle sizes can pose a challenge. Traditional vertical equipment often maxes out at a finished particle size of about 5 microns, necessitating careful media size selection.
Horizontal
Contrarily, horizontal mills, with their horizontal tubular grinding chamber, offer distinct advantages for wet grinding applications. The agitator shaft with disks is centrally placed, but the energy transfer happens from the media to the fluid, not by the disks, resulting in uniform media distribution and minimized physical attrition.
Such machines offer a host of benefits in wet milling:
- Efficient use of small media, ranging from 0.25mm to 2mm
- Significant reduction in product loss
- Enhanced color strength, gloss durability, and yield
- Up to 300% reduction in process time
- About 5% reduction in raw material costs
- Minimal contamination, solvent loss, and clean-up
- Resistance to abrasion
- Low operation, control, and maintenance requirements
- Consistent and predictable performance
The choice between vertical and horizontal mills depends on the specific application. Horizontal ones generally outperform in wet grinding applications due to their efficient media usage and superior reduction in product loss, among other benefits. Conversely, vertical models might be the preferred choice for tasks requiring high precision.
Allwin Machine & Equipment Co., known for its credibility in the market, provides high-quality Bead Mill Machines for wet grinding. Their range of mill solutions are expertly designed to cater to diverse grinding needs.
Selection of Separation Methods
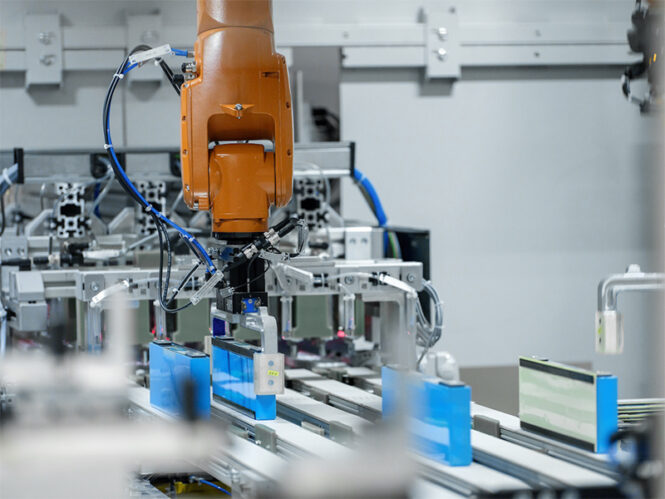
In bead mills, choosing the right separation method is critical, as it impacts the processing goal and the media size used. Three main methods exist: slit separation, screen separation, and centrifugation, each suited to specific bead size ranges and offering unique pros and cons.
Slit Separation
Slit separators work through a narrow gap at the slurry exit, which is ideal for beads of 0.3mm or larger. The separation process struggles with smaller media, leading to potential blockages. However, it performs stably for highly viscous slurries, with minimal bead leakage.
Screen Separation
Screen separators use a mesh screen, separating beads of 0.1mm or larger. This method has a larger slurry passage area, allowing smaller beads than the slitting method. However, with particles smaller than 0.1mm, a finer screen is needed, leading to a risk of clogging. It’s less suitable for high-viscosity slurries due to this tendency to clog.
Centrifugal Separation
Utilizing centrifugal force, centrifugal separators distinguish beads from the slurry mixture. Their unique design nullifies the threat of blockage, positioning them as an optimal choice for handling tasks related to microbead processing. This includes tasks like dispersing particles sized in the submicron and nanometer range.
Concluding Remarks
By understanding the inner workings of bead mills and recognizing the differences between horizontal and vertical ones, industry professionals can leverage these machines to meet various application demands.
Whether the task involves grinding large particles into smaller ones, dispersing particles into a liquid medium, or processing materials on a nanometric scale, bead mills offer a solution. Through comprehensive knowledge of bead size, milling operation, separation methods, and the differences between constructions, operators can achieve optimal dispersion and grinding results.
By adhering to these principles, industries can continue to innovate and excel, pushing the boundaries of their sectors while delivering high-quality products to the end-users.