Hydraulic systems are considered some of the most reliable components used in industrial machinery. The system is simple, and consists of fewer parts, hence making it more practical than other alternatives. But like any machine, hydraulics can also fail. And these failures aren’t only inconvenient, but also costly. As such, every hydraulic system user needs to know the common causes of failure and what to do to prevent these from happening.
How do you know that the hydraulic system is failing?
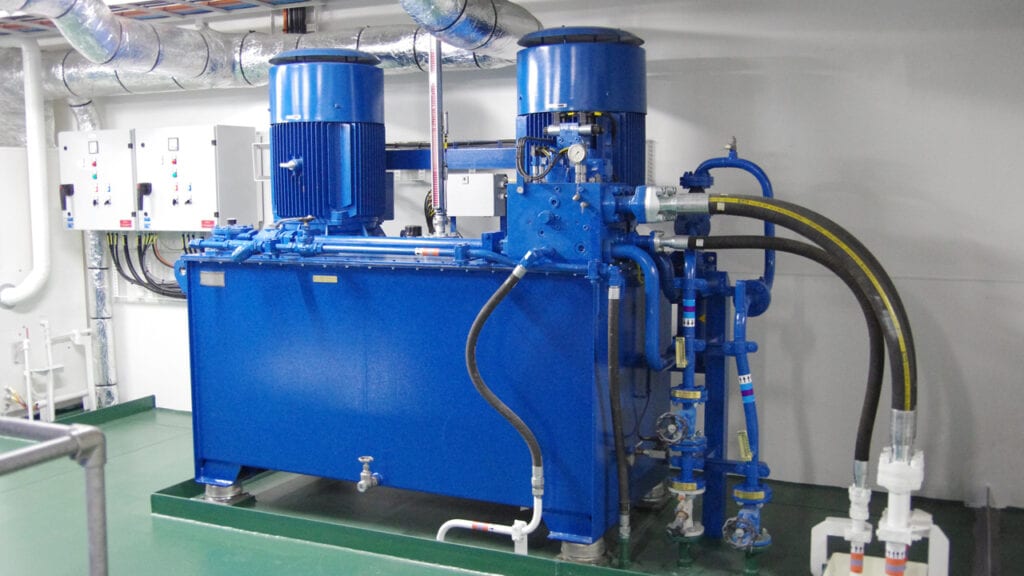
According to www.hydraproducts.co.uk, it’s easy to spot when a hydraulic system is failing. Some of the most common signs include overheating, slow operation, and low pressure. If you regularly conduct proactive maintenance, it’s possible to prevent system failure. But, it’s also possible to overlook the early indications of a problem. First, let’s discuss the common signs and symptoms that indicate a problem with the hydraulic system.
- Abnormal noises are coming from the machine. Hydraulic machines make noise as part of regular operation. But, anytime the noise becomes too loud or prominent, it should be a cause for alarm. Watch out for loud knocking or banging sounds as the pumps compress and decompress fluid. These loud sounds could indicate that the system is contaminated with air or water.
- Unusually high temperature. The normal temperature of a hydraulic system shouldn’t be higher than 82 degrees Celsius. It’s critical to monitor the temperature at different intervals to ensure that the system doesn’t overheat. There are several reasons why a hydraulic system overheats. For instance, when the fluid becomes too viscous, it loses the ability to release heat. Obstructions can also be another cause of overheating.
- Slow operation. One of the first signs to look out for is the machine’s performance. Any indication that the system is slowing down should be checked immediately. A slow hydraulic system could mean that fluid flow is also compromised.
Now that we’ve discussed the common signs of hydraulic system failure let’s focus on the causes of hydraulic system failure.
Contamination
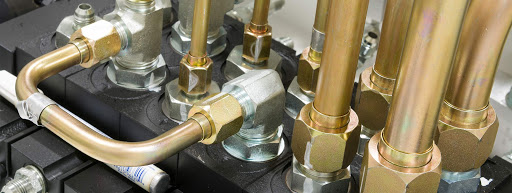
Contamination by air or water accounts for over 80% of hydraulic system failures. And the root causes of this issue include unstable temperature, system breach, or a faulty pump. Air contamination happens when air enters the system. When air contaminates the system, it may result in severe damage as it could wear out components. Contamination can happen in two ways:
- Aeration. This phenomenon occurs as air enters from the outside through a system breach. If the system has any leaks, aeration is quite common.
- Cavitation. The hydraulic fluid contains a small percentage of air that could implode as the pump pulls it out. Over time, this implosion will damage the system’s internal components, which you can quickly identify when you hear a whistling or whining noise.
In addition to air contamination, water contamination is another common issue encountered by hydraulic system users. The unstable temperature may result in condensation where water seeps into the system through small cracks and leaks.
Quality and level of hydraulic fluid
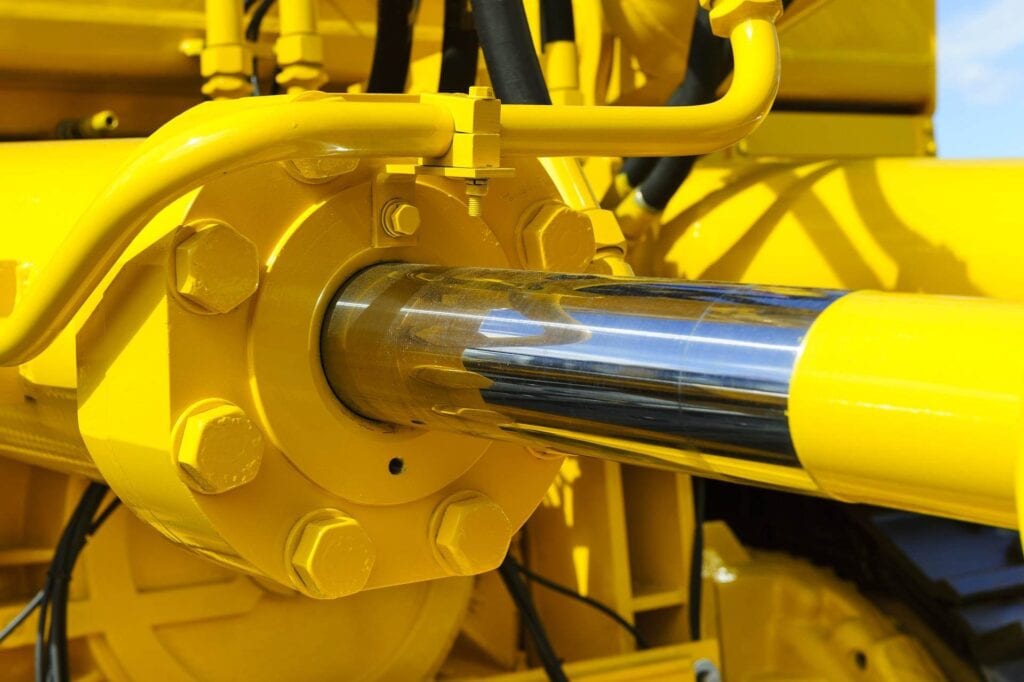
The quality of hydraulic fluid, as well as its level, will impact the system’s performance. When the fluid level is lower than usual, air contamination may occur and eventually lead to overheating. Also, there are different kinds of hydraulic fluid compatible with various applications. For instance, oil-based fluids are ideal for applications that are exposed to high-temperature conditions.
Unstable temperature
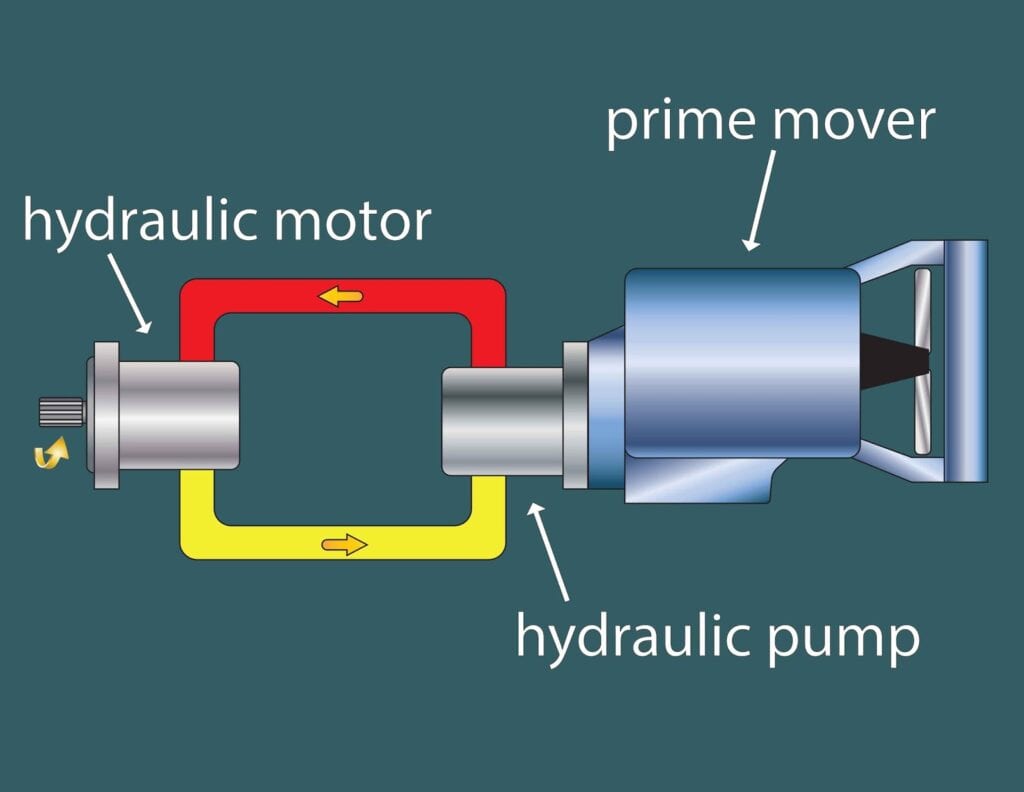
When the system is either too cold or too hot, problems will occur. For example, higher than normal temperature results in fluid thinning, which reduces lubrication and results in leaks. Extreme heat can also cause the fluid to oxidize and cause build-up inside the system. Apart from internal factors that may cause an unstable system temperature, the working environment also plays a crucial role. It’s essential to keep the temperature in check and keep it within the recommended range.
Human error
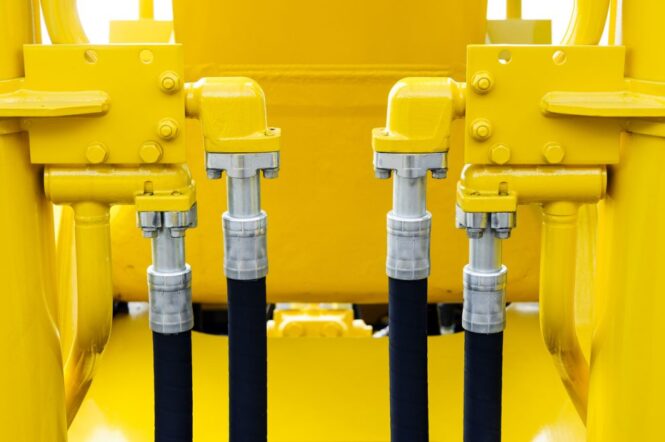
Last on this list of common hydraulic system failure causes is human error. Unfortunately, human intervention will always have an impact on how machines work. Incorrect installation is likely to happen when the person working on the system isn’t experienced. Another problem could be installing parts that aren’t compatible with the machine. Lastly, neglect, improper use, and lack of maintenance are all associated with human error that are typical causes of hydraulic system problems.
Tips for proactive hydraulic system maintenance
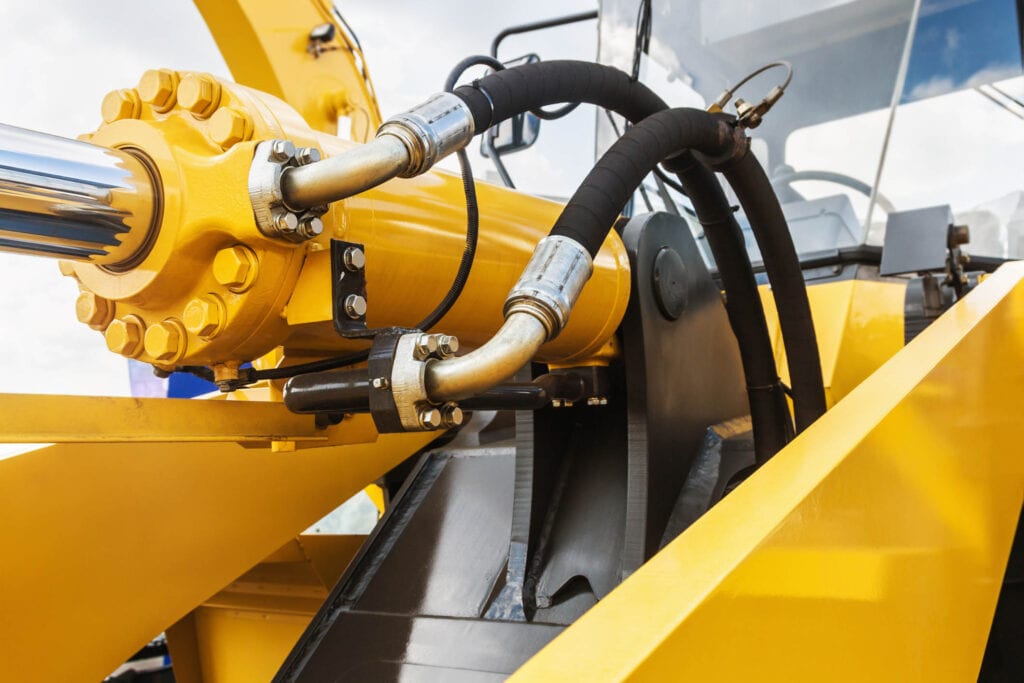
Knowing the signs and causes of hydraulic system failure is essential to the system’s smooth operation. Moreover, it’s also vital to conduct preventive maintenance steps to prolong optimal working conditions. Here are tips on what every hydraulic system user needs to do for maintenance.
- Keep temperature and fluid viscosity at ideal levels. As the hydraulic system operator, it’s your responsibility to know the minimum and maximum operating temperature and fluid viscosity in relation to the external working environment. These factors matter because hydraulic fluids can contain different types of additives suitable for various conditions.
- Keep the fluid clean. To prevent fluid contamination, filters should be replaced regularly. Also, the type of filter used should be compatible with the particle size and fluid additives.
- System settings should follow manufacturer recommendations. The system should always operate according to the manufacturer’s specifications. Also, it’s vital to follow the recommended maintenance schedule and avoid any deviations to the settings as much as possible. Following what the manufacturer recommended will ensure that you can keep the warranty active within the allowed time frame.
- Make replacements proactively. Although there’s a recommended schedule when parts are supposed to be replaced, it would also help if you proactively replace them before the schedule, especially when the system is heavily used. Wear and tear vary according to the working condition; hence your discretion is critical in deciding the best time to replace components.
When things go wrong despite following these maintenance tips, the first thing you need to do is conduct a complete system assessment. The assessment should give you further insight into which procedures you need to change and what you can do later on to prevent the system failure.